Testing Process
We'll Prove your Product Meets the Standards.
We start by understanding your quality standards. We comply with ASTM standards and we are NADCAP accredited for Florescent Penetrant, Magnetic Particle and Radiography Film. The standards that your parts need to meet will determine the process that we use. Below are the processes we specialize in performing.
NADCAP Accredited Testing Process
NADCAP (National Aerospace & Defense Contractors Accreditation Program) accreditation is a quality management system used to assess and certify suppliers of products and services in the aerospace and defense industries. It is a globally recognized program that ensures conformity to industry standards, specifications, and customer requirements. NADCAP accreditation is granted to suppliers who meet the program's stringent requirements, demonstrating their ability to consistently deliver high-quality products and services that meet the distinctive needs of the aerospace and defense industries.
ASTM Standards for Metal Testing Processes
ASTM (American Society for Testing & Materials) International is an organization which develops and publishes technical standards for materials, products, systems, and services. ASTM standards include testing methods, material properties, and safety requirements. At American Metal Testing, all our testing processes adhere to ASTM standards, ensuring your components are thoroughly examined.
Fluorescent Penetrant Inspection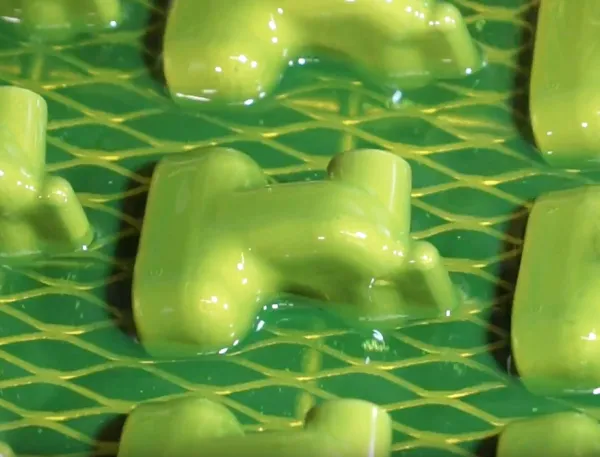
When your quality standard requires a surface free from tiny cracks, inclusions, or other surface defects that are not detected with a visual inspection, fluorescent penetrant inspection will allow the detection of such imperfections on most non-porous materials. The part is cleaned, and a colored dye solution is applied to the part's surface. The dye is suspended in penetrating oil and freely flows into these surface imperfections. When our special developer is applied, the defects are clearly indicated.
A similar method suspends fluorescent powder in penetrating oil. This brightly colored film covers the parts, and the penetrant finds its way into any defects. The part is dusted with drying powder, and the fluorescent solution is drawn from the defect. A visual inspection is done in an ultraviolet-lighted environment, clearly revealing the defects as they glow.
Generally, dye-penetrant testing techniques will identify defects on the surface of the casting and will not detect internal porosity or shrinkage that is not open to the surface. However, FPI can detect hairline cracks, rounded indications for porosity, or gas on the casting surface. FPI methods are less expensive than radiographic testing.
Magnetic Particle Inspection
Magnetic particle Inspection (MPI) detects surface and slightly subsurface discontinuities in ferromagnetic materials such as iron, nickel, cobalt, and others made from these alloys. A high-amperage, low-voltage current is passed through the part, which establishes a magnetic field. Magnetic flux is introduced to the part. Since cracks and defects have different magnetic properties than those of the surrounding material, their presence causes distortion by interrupting the magnetic field, thereby indicating the shape and position of the crack or void.
The piece can be magnetized by direct or indirect magnetization. Direct magnetization is when the electric current passes through the part and a magnetic field is formed in the material. Indirect magnetization is when a magnetic field is applied from an outside source. The magnetic lines of force are perpendicular to the direction of the electric current which may be either alternating current (AC) or some form of direct current (DC) (rectified AC).
Magnetic particle inspection is quick, inexpensive and sensitive to particularly shallow (0.003 in.) defects, surface cracks and other lineal indications.
Radiographic Testing
Radiographic inspection, or X-ray metal testing, is the best nondestructive method for detecting internal defects and hidden flaws, including shrinkage and inclusions. This process allows us to look inside the part with short wavelength electromagnetic radiation (high energy photons) to penetrate various materials. And the radiograph serves as a permanent record of the part quality that can be reviewed by multiple personnel.
In the radiographic inspection method, a part is exposed to ionizing radiation from an x-ray tube. The component absorbs some of the radiation, and the remaining portion of the radiation exposes the radiographic film. Dense material withstands the radiation penetration, so the film is exposed to a lesser degree in those areas, giving the film a lighter appearance. Less dense materials allow more penetration and correlates to darker areas on the film. Any hole, crack or inclusion that is less dense than the part’s alloy is revealed as a dark area.
Casting thickness and density will affect the range of inspection possible, depending on the energy level of the radiation.
Contact AMT for NADCAP Accredited Metal Testing Processes
Contact us today to learn more about our NADCAP-accredited metal testing processes that comply with ASTM standards. At American Metal Testing, we strive to maintain the highest quality in all non-destructive testing and failure analysis of metal components, machine parts, and metal casting, ensuring your metal parts are safe, reliable, and free from defects. For all your metal testing needs, trust American Metal Testing.
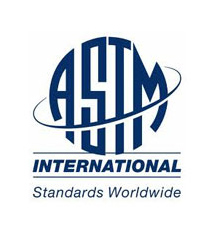