Non-Destructive Testing for Aerospace Applications
Non-destructive testing (NDT) methods are essential for enhancing the safety of aerospace manufacturing and maintenance processes. Non-destructive testing methods are used to inspect aircraft components and parts without causing damage to the integrity of the piece being tested. NDT inspection processes detect surface or subsurface flaws, including cracks, corrosion, and other defects that can occur during aerospace components' manufacturing or operational lifecycle. By using non-destructive metal testing services, we help ensure that aerospace parts and components are safe and ready for service.
Non-Destructive Inspection Methods for Aviation
At American Metal Testing, we specialize in high-performance non-destructive metal testing processes, including Magnetic Particle Inspection, Fluorescent Penetrant Inspection, and Radiographic Inspection. All our testing processes are certified by the American Society for Testing & Materials (ASTM) and are designed to find defects and discontinuities in metal components used in critical applications.
Fluorescent Penetrant Inspection for Aerospace Components
Liquid Fluorescent Penetrant Testing is a non-destructive testing method used to detect surface-breaking flaws on metal components used in aerospace applications. A fluorescent dye penetrant is applied to the component's surface, seeping into any surface cracks, porosity, or other defects. The excess penetrant is removed, and a developer is applied to the surface. The developer draws the penetrant out of flaws and creates a visible indication on the surface, inspected under ultraviolet light. The inspection process reveals any surface-breaking flaws, allowing inspectors to evaluate the component's quality and integrity.
Radiographic Testing for Aerospace Components
Radiographic Film Testing, or X-ray testing, is an NDT process that can be applied to metal and non-metal materials. This method inspects aerospace components for cracks, voids, inclusions, and other defects. The process involves exposing the component to X-rays which penetrate the metal and produce an image on a film or digital detector. The image reveals any internal discontinuities within the metal, allowing inspectors to evaluate the component's quality and integrity.
Magnetic Particle Inspection for Aerospace Components
Magnetic Particle Testing is another method for inspecting aerospace components made from ferromagnetic metals, including iron and steel. The part is magnetized, and a suspension of magnetic particles is applied. A magnetic flux leakage will disrupt the field and draw the magnetic particles to any discontinuities. The component is then inspected under ultraviolet light and evaluated for imperfections.
NADCAP Certified Non-Destructive Metal Testing Services for Aircraft
As a non-destructive testing laboratory, American Metal Testing holds NADCAP accreditation. This recognition reflects our dedication to performing thorough NDT processes, ensuring consistent outcomes, and outstanding quality control. Our certification enables us to serve prominent aerospace manufacturers, including Boeing, Parker Aerospace, UTC Aerospace Systems, and more.
Additionally, our testing services meet requirements established by several leading industrial regulation organizations, including ASTM, AMS (Aerospace Material Specifications), and more. Our state-of-the-art in-house equipment is calibrated and traceable to the National Institute of Standards & Testing (NIST).
Contact Us for Aerospace Inspection Services
Contact American Metal Testing to learn how we can provide your aerospace components with premium NDT inspection services. You can also request a quote for pricing information for your application's requirements. For all your industrial metal testing requirements, choose Americant Metal Testing.
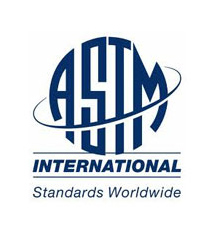